
WEEK 2
QUICK CRIT
I made a thing...
​
It's an audible tin of panettone. To be honest, it didn't quite work out as I intended. I wanted to use springs and contact microphones to create an interactive installation to capture voices from outside of the tin and reproduce them with the texture, materiality, and space of the thin, metal tin. It was very good at picking up the sounds that construct the tin, but, as I said, it didn't respond much to voices, unless one was very close to it.
Slightly disappointing.
​
The critique was very good. We spoke about adding strings to the installation. Guitar strings or something similar that could be either lightly stroked or aggressively plucked to create a sound. Essentially, this project will be a funny looking, out of tune guitar if I carry on with it. Which I will. We also spoke about adding more tins with different types of microphones to evolve it into a performance piece. I'm not a huge performer when it comes to doing things in front of people, but I could create the instrument and let someone else play with it.
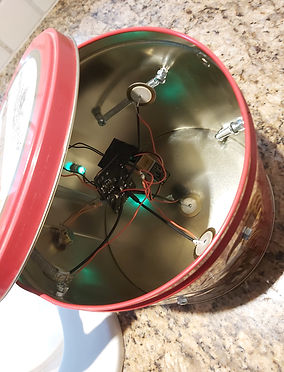
UPDATE #1:
Since this session, I have been thinking about how to improve on my piezo mic thing. One thing I came across was to create my own piezos, so that I am not relying on too many pre-constructed components. Researching this led me to piezoelectric materials and a video on youtube about how to create the crystals that are used to make a contact microphone. Susanna Cruser published a video showing how to make a piezoelectric material called Rochelle Salt (sodium-potassium tartrate) by using sodium bicarbonate and cream of tartar (potassium bitartrate).
​
Now I need to figure out how to stick the Rochelle Salt crystals to brass. I can't find anything online, so I will just get some brass, make the rochell salt and figure it out.
​
UPDATE #2:
​
I tried to make Rochelle Salts... Apparently, my ingredients weren't pure enough, so I am in the process of researching which would be the best to buy. What happened was it did actually crystalise, but they came out wayyyyy too small. Buying more, and higher quality ingredients should allow me to make large crystals from which I can make some cool sounds.
​
UPDATE #3
​
Have not been able to redo the experiment. Even if I had been able to, the next step of drying, crushing, and somehow fusing the crystals to brass is beyond me. I have decided to just experiment with pre-made piezo microphones and not waste time creating something that is, honestly, more expensive to make than to buy.



While trying to create my own piezoelectric crystals was a failure, it was a process that I do not regret. It provided a basis for experimentation in a field that I am profoundly unfamiliar with. I believe that I could have progressed with this had I researched more, or communicated with some manufacturers of piezoelectric materials. All in all, it was a personal achievement to get as far as I did, adding to my current interest in sound and my newfound perspective into how audio components work.
​
With this in mind, there are people in the world that have created microphones out of piezoelectric crystals. These microphones are not very expensive at all (£0.79p at RS Components) so making the microphones from scratch would have cost a lot more.
​
This project found its natural endpoint
right around the moment I thought
I needed to start making my own microphones.
​
​
​
FIN